Gauges are crucial in manufacturing, ensuring smooth processes and high-quality products by measuring parameters like pressure, temperature, level, and flow. They provide critical data for decision-making and maintaining efficiency. This guide explains the importance and role of industrial gauges.
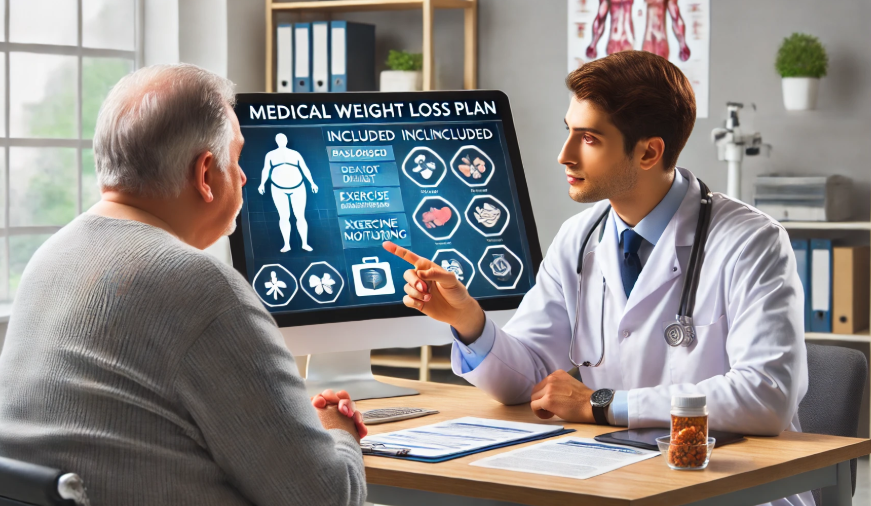
Types of Industrial Gauges
Pressure Gauges
Pressure gauges are vital in monitoring and controlling the pressure within a system. They help prevent over-pressurization, which can lead to equipment failure or safety hazards. Common applications include hydraulic systems, gas cylinders, and refrigeration units. Pressure gauges come in two main types—Bourdon tube gauges and digital pressure gauges.
Temperature Gauges
Temperature gauges are used to monitor and maintain optimal temperature levels in various industrial processes. They are crucial in industries like food processing, chemical manufacturing, and power generation. Types of temperature gauges include thermocouples, resistance temperature detectors (RTDs), and bimetallic strips. Among these, type K thermocouples from Temp Pro, or a similar other firm, can be beneficial for their durability and ability to withstand harsh industrial environments, This can make it suitable for broad range of applications and processes to improve both efficiency and safety.
Level Gauges
Level gauges measure the amount of liquid within a tank or vessel. These gauges are essential in industries such as oil and gas, pharmaceuticals, and water treatment. Some common types are sight glass level gauges, magnetic level gauges, and ultrasonic level sensors.
Flow Gauges
Flow gauges measure the rate at which a fluid or gas moves through a system. Accurate flow measurement is crucial for maintaining process efficiency and ensuring product quality. Types of flow gauges include turbine flow meters, Coriolis flow meters, and thermal mass flow meters.
Selecting the Right Gauge
Environmental Conditions
When selecting an industrial gauge, consider the environmental conditions it will be exposed to. Factors like temperature extremes, humidity, and exposure to chemicals can affect the performance and longevity of the gauge. Choose materials and designs that are compatible with the specific environment.
Material Compatibility
The gauge material must be compatible with the medium it will measure to prevent corrosion or contamination. For example, stainless steel is a popular choice for its durability and resistance to corrosion, making it suitable for various applications.
Accuracy Requirements
Different applications require different levels of accuracy. Ensure the gauge you select meets the precision required for your specific process. Higher accuracy gauges often come at a higher cost, so balance accuracy needs with budget constraints.
Installation and Maintenance
Best Practices for Installation
Proper installation is crucial for accurate gauge performance. Ensure that gauges are installed in locations that provide easy access for monitoring and maintenance. Avoid placing gauges near high-vibration areas or extreme temperatures, which can affect their readings.
Calibration
Regular calibration is essential to maintain the accuracy and reliability of industrial gauges. Calibration involves comparing the gauge readings with a known standard and making necessary adjustments. Establish a routine calibration schedule based on manufacturer recommendations and industry standards.
Routine Maintenance
Routine maintenance extends the lifespan of industrial gauges and ensures consistent performance. Regularly inspect gauges for signs of wear, corrosion, or damage. Clean the gauges as needed and replace any faulty components promptly.
Future Trends in Industrial Gauges
Smart Gauges
The future of industrial gauges lies in smart technology. Smart gauges equipped with IoT capabilities can provide real-time data monitoring, remote access, and predictive maintenance insights. These features enhance operational efficiency and reduce downtime.
Advanced Materials
Advancements in material science are leading to the development of more durable and corrosion-resistant gauges. These new materials extend the lifespan of gauges and improve their performance in harsh environments.
Integration with AI and Machine Learning
Integrating industrial gauges with AI and machine learning algorithms can provide deeper insights into process optimization. AI-driven analytics can predict potential issues before they occur, allowing for proactive maintenance and improved decision-making.
Conclusion
Industrial gauges are the unsung heroes of manufacturing, playing a critical role in monitoring and controlling various processes. From pressure and temperature to level and flow, these devices ensure operational efficiency, safety, and product quality.